The Science and Technology Behind the Production of Life-Saving Medical Devices
Hypodermic needles play a crucial role in the medical field, as they’re used to administer medications and draw blood samples. They’re designed to deliver substances into the body with minimal pain and discomfort for patients.
The process of making hypodermic needles involves several steps, including selecting materials, forming cannulae, grinding bevels, attaching hubs, and sterilizing the final product.
By understanding this process more thoroughly, you’ll gain a deeper appreciation for these vital instruments and their importance in healthcare settings.
In this article, we’ll delve into each step involved in manufacturing hypodermic needles, highlighting key considerations along the way to ensure optimal performance and patient safety.
Different Types of Hypodermic Needles
Hypodermic needles come in various designs and sizes to cater to specific medical applications. Here is an overview of some common types of hypodermic needles, including the Hydra needle.
Standard Hypodermic Needles
These are the most common type of hypodermic needles used for a wide range of applications, including intramuscular, intravenous, and subcutaneous injections. They are available in different gauges (diameters) and lengths to accommodate various patient needs and injection sites.
Insulin Needles
Insulin needles are specifically designed for insulin injections in patients with diabetes. They are usually shorter and thinner than standard hypodermic needles, ensuring minimal discomfort during the injection process.
Safety Needles
Safety needles feature built-in safety mechanisms, such as retractable or shielded tips, to minimize the risk of needlestick injuries and contamination. These needles are particularly useful in healthcare settings where frequent injections are administered, and safety is a top priority.
Blunt Fill Needles
Blunt fill needles have a non-penetrating, rounded tip designed for drawing medication from vials without the risk of coring (puncturing the rubber stopper). These needles are commonly used by healthcare professionals to prepare medications before administering them using a separate, sharp needle.
Spinal Needles
Spinal needles are designed for lumbar puncture procedures, where cerebrospinal fluid is collected or medications are injected into the spinal canal. These needles have a unique tip design, such as the Quincke or Whitacre tip, which minimizes tissue damage and post-procedure complications.
Hydra Needles
Hydra needles are innovative, multi-needle devices used for various aesthetic treatments, such as microneedling, mesotherapy, and dermal infusion. These needles have multiple, ultra-thin needle tips arranged in a cluster, allowing simultaneous delivery of medications or serums into the skin while minimizing discomfort. Hydra needles are popular among skincare professionals for their ability to provide efficient and consistent treatment results.
Understanding the differences between these types of hypodermic needles is essential for healthcare professionals to select the appropriate needle for each medical application, ensuring patient safety and comfort during injections and other procedures.
Material Selection For Needle Production
Selecting the appropriate material for hypodermic needle production is crucial in ensuring needle durability and corrosion resistance. A variety of materials can be utilized, but stainless steel, specifically type 304 or 316, has been proven to provide optimal results in terms of strength, ductility, and biocompatibility.
Stainless steel meets several important criteria including being readily available, cost-effective, easy to process through manufacturing techniques such as cold drawing and swaging, and highly resistant to environmental factors that could lead to corrosion. It is essential to understand that various medical applications require different levels of performance from a hypodermic needle; therefore, choosing the right material becomes paramount.
For instance, while surgical needles demand greater physical strength for suturing tissues under tension, diagnostic needles necessitate thinner walls for ease of penetration during sample collection. In either case, by selecting an appropriate grade of stainless steel as the primary construction material for these devices ensures reliability and longevity without compromising patient safety or clinical outcomes.
Forming And Shaping The Cannula
Having discussed the importance of selecting appropriate materials for needle production, it is now crucial to delve into the process of forming and shaping the cannula.
The cannula is a vital component in hypodermic needles as it ensures smooth penetration through tissue while minimizing patient discomfort.
An ideal cannula curvature ensures that the needle glides effortlessly through tissues without causing unnecessary trauma or damage. This is particularly significant when injecting substances like medications or drawing fluids during various medical procedures.
To achieve this, manufacturers employ advanced techniques such as laser cutting or cold forming to create precise shapes and configurations tailored to specific applications.
On the other hand, needle flexibility refers to its ability to bend without breaking or deforming under pressure.
Appropriate flexibility enables easier insertion into different body parts at various angles while reducing risks associated with breakage inside patients’ bodies.
Grinding Bevels And Attaching Hubs
Visualize a skilled technician meticulously grinding bevels and attaching hubs to create the perfect hypodermic needle. This vital process requires precision, expertise, and an understanding of various bevel types and hub designs in order to produce needles that are effective for their intended medical applications.
Grinding bevels involves shaping the needle tip to achieve different angles and cutting edges based on specific requirements:
Bevel Types:
- Regular (R) bevel: most common type, featuring a sharp slant at the needle’s end for easy insertion into soft tissue.
- Short (S) bevel: similar to R-bevel but with shorter slant; ideal for denser tissues or when minimal penetration is needed.
- Intradermal (ID) bevel: specifically designed for intradermal injections due to its shallow angle and longer point length.
- Huber Point (HP): this non-coring design consists of a curved cutting edge that reduces trauma during insertion while minimizing leakage around the puncture site.
Once the appropriate bevel has been ground onto the needle, it must then be securely attached to a compatible hub. The selection of suitable hub designs is crucial as they facilitate connection between the needle shaft and syringe barrel or other medical devices. Some key aspects to consider include material compatibility, ease of use, sterility maintenance, and patient comfort.
Hub Designs:
- Luer Lock Hubs: these secure locking mechanisms prevent accidental disconnection from syringes during procedures.
- Slip Tip Hubs: simple friction-based connections allowing rapid assembly/disassembly without added bulk.
- Pen Needle Hubs: compact options optimized for insulin pen injectors with integrated safety features such as retractable needles or automatic shielding systems.
Mastering both grinding techniques and selecting appropriate hub designs play essential roles in producing high-quality hypodermic needles. It is important not only for ensuring the effectiveness of medical treatments but also in providing patients with a comfortable experience during various healthcare procedures.
THE PERFECT NEEDLES FOR YOUR PATIENTS. CODE “20OFF” FOR 20% OFF YOUR FIRST ORDER!
FACE Med Store supplies countless doctors and clinics with all their supplies, including top-of-the-line hypodermic needles. Get your hypodermic needles at 20% off today!
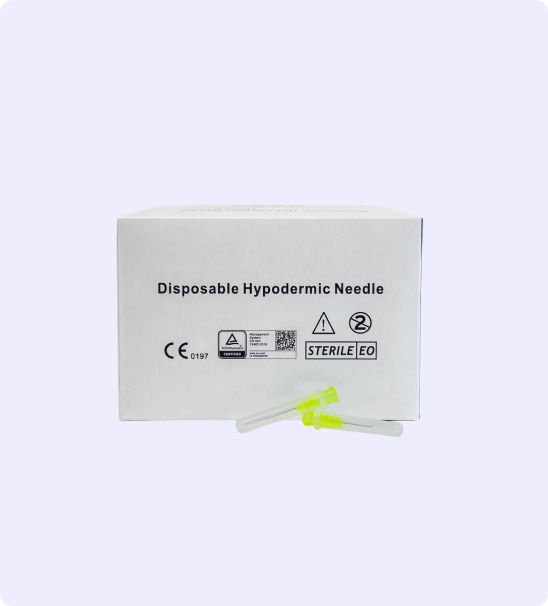
Sterilization And Quality Control
Needle sterilization and quality control play a crucial role in ensuring the safety of patients while using hypodermic needles. Not only do these processes protect against infections, but they also help maintain the overall integrity of needles throughout their lifecycle.
Infection prevention is paramount when it comes to needle usage in medical settings. One key aspect of this process involves proper needle disposal after each use. The following table outlines some important factors to consider for effective infection prevention:
FACTOR | IMPORTANCE | EXAMPLE |
Sterilization | Eliminates harmful pathogens from the needle | Autoclaving |
Proper Needle Disposal | Prevents accidental injury and reuse | Sharps containers |
Quality Control Checks | Ensures consistent manufacturing standards | Visual inspection for defects |
Storage Conditions | Protects needles from contaminants | Clean, dry environment |
Staff Training | Promotes safe handling and adherence to protocols | Regular workshops on safety measures |
FAQs
Q: What is the manufacturing process for creating hypodermic needles?
A: The production process for hypodermic needles involves several steps, including selecting the appropriate stainless steel material, cutting needle tubes to specific lengths, grinding and polishing the needle tips, assembling the needle with a syringe or injection device, sterilizing the final product, and packaging the needles for medical use.
Q: How do needle gauge and length vary among different types of hypodermic needles?
A: Hypodermic needles come in a wide range of gauges (diameters) and lengths to accommodate various medical applications. Needle gauge typically ranges from thin needles (higher gauge numbers) for subcutaneous injections to thicker needles (lower gauge numbers) for intramuscular and intravenous injections.
Q: Are there different types of needles for specific medical purposes?
A: Yes, various types of needles cater to specific medical needs. For instance, blunt needles are used for non-penetrating procedures, while specialized insulin needles are designed for insulin injections. Other needle types include those for intramuscular, intravenous, and subcutaneous injections.
Q: What is the difference between disposable and reusable needles?
A: Disposable needles are single-use devices that are discarded after use, reducing the risk of contamination and infection. Reusable needles, on the other hand, are made of durable materials like stainless steel and require proper sterilization between uses.
Q: How has injection molding technology improved the production of disposable syringes?
A: Injection molding has streamlined the manufacturing process for disposable syringes, allowing for mass production of high-quality, consistent, and cost-effective medical equipment. This technology enables precise control over the size and shape of the syringe components, ensuring optimal performance during injections.
Q: Are there any innovations in hypodermic needles that help alleviate the phobia of needles?
A: Yes, new developments in needle technology, such as rapid injection devices and ultra-thin needle designs, aim to minimize pain and anxiety associated with traditional injections. These innovations can help reduce the phobia of needles, particularly for patients who require frequent injections or have a low pain tolerance.
Conclusion
It’s essential to carefully select materials and follow precise manufacturing processes when producing hypodermic needles.
Ensuring a high level of quality control is crucial for patient safety and comfort.
As medical professionals, our duty is to provide the most reliable tools in healthcare.
By understanding the intricacies involved in needle production, we can better appreciate the importance of adhering to strict standards throughout every step of the process.